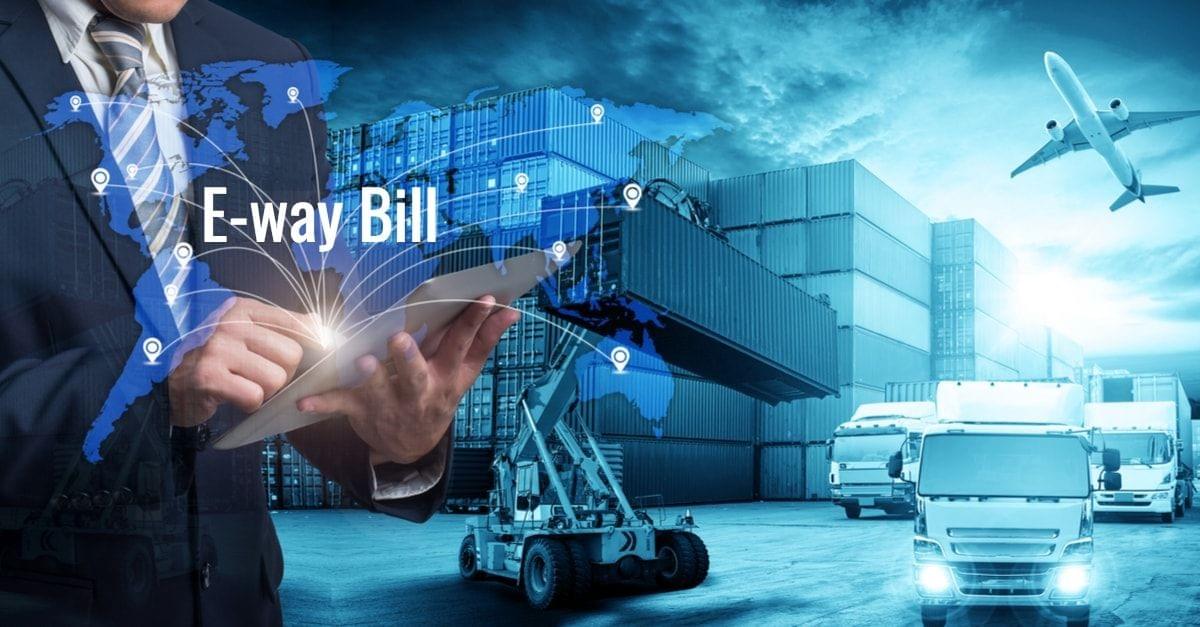
Autonomous trucks, communicating machines, products from the 3D printer - and everything is networked with everything. What is in store for us?
The future may not have begun yet, but it is already very close: In a few years from now, we will see columns of autonomous trucks on our roads.
In the future, we may see platooning of trucks across highways. Truck manufacturer Daimler already tested it once. "Platooning" is the technical term for it, from the English "platoon," which means a military train or a column. In truck platooning, the vehicles rush across the autobahn at a speed of 85 at just 15 meters. The digital technology of the future makes it possible; for example, it only needs a fraction of the human reaction time to initiate braking. The platoon "communicate" with each other and adjust the distance depending on the situation. The driver is only there to intervene in an emergency and keep an eye on the general traffic situation.
Digitization of work processes, the networking, and interaction of machines and autonomous control systems, as they are already known under the term "Industry 4.0," will also affect logistics. Driverless trucks are just the most spectacular part of this "Logistics 4.0", as experts already call it because they are the most effective. But all other areas such as warehouse logistics, procurement, and distribution of production logistics are also affected.
Logistics 4.0 includes "the networking and interlinking of processes, objects, supply chain partners (suppliers, manufacturers, wholesalers, retailers, and logistics service providers) and customers with the help of information and communication technologies with decentralized decision-making structures." These self-regulating objects and processes communicate with each other and with people, learn from each other, make independent decisions, monitor and report environmental conditions (e.g. temperature, time, location, speed, load), and control logistics processes. Logistics 4.0 will thus become the basis for holistic digital supply chain management.
Take a 3D printer; for example, The computer-controlled, layer-by-layer construction of three-dimensional workpieces will also have a lasting impact on tomorrow's logistics. As logisticians, individuals will have to think carefully about which parts they will store for the customer and which they will produce as a service with printers. Researchers from Renault Trucks reported at the end of January that they had already developed a complete engine for manufacture using 3D printing and had already printed some parts. Among other things, they expect a weight reduction of around 25 percent, which would, for example, have a positive effect on fuel consumption.
Significant energy savings could also be achieved with the already mentioned platooning of trucks - simply because they always move in the slipstream due to the small distance to the vehicle in front. Platooning advocates hope that this could change in the foreseeable future. Because already today, 1.2 million trucks drive on German autobahns every day, transporting 4.1 billion tons of goods. According to the Shell commercial vehicle study, this amount should increase to 4.8 billion tons by 2040.
Freight railways test the Internet of Things
This means that they can always see where the wagons and goods are and keep their customers updated. As shocks often occur during maneuvering and loading, which in the worst case can damage freight wagons and interests, a three-axis acceleration sensor in the networking hardware measures the strength, frequency, and exact position of these impacts and evaluates the corresponding data. The entire transport can thus be thoroughly documented.
Conclusion
In Industry 4.0, IT solutions for logistics are often seen only as building blocks for complete networking along the value chain. Production is usually the focus of considerations on Industry 4.0. Therefore, it is not surprising that terms such as "factory of the future" or "smart factory" are used synonymously and in a simplified manner for Industry 4.0.
Read also :
Check out portfolio related to logistics Industry :